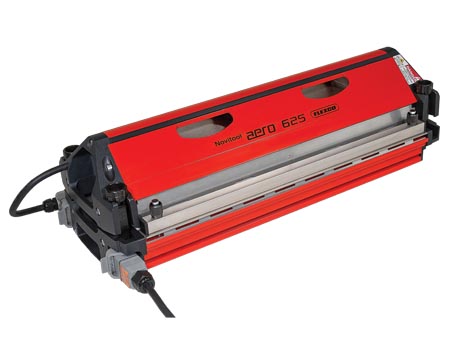
Industry
Food processing
Application
Conveying meat in refrigerated warehouse
Product
Novitool® Aero® Portable Splice Press
Objective
Reduce maintenance downtime
Make splice process more sanitary
Conveyor Detail
Polyurethane belting
Problem:
The maintenance team at a refrigerated warehouse was looking for a way to reduce downtime when splicing belts. Not only was downtime costly, but the heat generated from the press during the long cycle time was a problem in the refrigerated environment. They were also looking for a splicing method in which they could reduce the possibility of bacterial contamination that would make their warehouse unsanitary for food storage. Water-cooled presses took a lot of time to set up, splice, and tear down and often required several components being carted to and from the site. The water cooling system also presented a potential bacterial contamination source.
Solution:
The team decided to try the Novitool® Aero® Splice Press, an air-cooled press that completes endless splices in just 7 to 12 minutes each, which means less downtime for the system and less overall heat being generated in the refrigerated environment. The portability of the Aero Press was also attractive to the team. With fully integrated controls, an air compressor, thermocouples, electrical controls, and air cooling fans all built into the press, it meant that transporting the equipment to the jobsite was a simple process. An added benefit is that the press comes with a custom flight case to not only protect the press when not in use, but also for easy transport to the jobsite.
Result:
Splicing is now completed in a very short time, which is also very important because generating heat for a long period of time is not optimal in the refrigerated warehouse. The cooling system on the Aero Press requires no water tanks or hoses, removing the risk of contamination and conforming to hygiene regulations.