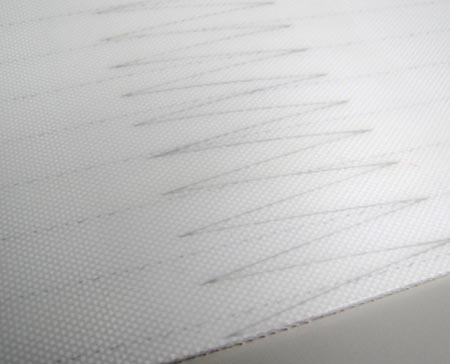
Industry
Agriculture/Hay Baling
Application
Endlessing Belts in a Tobacco Plant
Product
Novitool® Aero® Splice Press
Objective
Reduce downtime
Reduce risk of product contamination
Conveyor Detail
Two-ply Polyolefin belts
Problem:
The maintenance manager at a tobacco plant that produces approximately 35 million cigarettes per year was looking for a more efficient way to splice their belts. The tobacco plant maintenance crew had long been vulcanizing their belts using a water-cooled press. With this press, complete splice time, including set up, was two hours.
Solution:
Sample polyeofin belts were brought in and the Novitool® Aero® Splice Press was demonstrated for several members of the maintenance crew. The press only took 10 minutes to set up, and seven minutes to complete the actual splice. The maintenance manager was not only impressed by the time savings, but also by the fact that no water is required for cooling.
Result:
Shorter splice time, lighter equipment, and fewer components to haul around the plant were all benefits listed by the maintenance manager. Plus, the air cooling process of the Aero Press keeps moisture out of the process, which is important in a dry tobacco processing application in terms of product quality and reducing contamination. The time savings was most impressive, however, as the maintenance team saw an 86% reduction in time spent from set up to completion of the splice. He also noted that while the Aero Press is lightweight and portable, it still provides a flat, consistent splice.