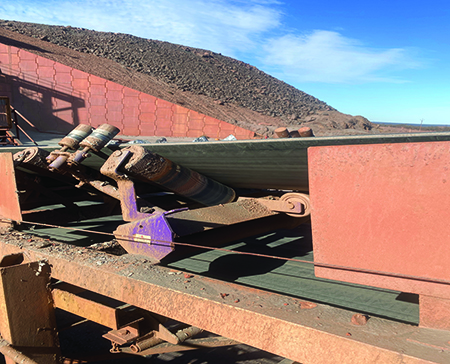
Industry
Iron Ore
Application
Primary Crusher
Product
PT Max™ Belt Trainer
Objective
Eliminate belt mistracking
Maximise safety
Reduce spillage
Stop belt damage
Conveyor Details
1500mm belt width, running at 5m/sec
Problem:
An Australian Iron Ore site had stationary trackers installed that did not move with the belt, resulting in a multitude of problems. Due to the trackers being completely stationary, the guide rollers eventually began to wear into the belt, causing severe damage. This resulted in not only belt damage, but the rapid change out of the guide rollers and thousands of dollars spent on parts and labour. On top of this, the trackers were completely ineffective, which lead to a myriad of other issues along the conveyor line. Most of these issues were surrounding the amount of product falling off the belt. This spillage would pile up underneath and beside the conveyor and would require several workers to manually shovel away the excess product, creating safety concerns for the mine.
Solution:
After working closely with the mine, Flexco Territory Manager, Jayden Baker recommended the PT Max™ Belt Trainer. Unlike the previous product, the PT Max features patented “pivot and tilt” technology. This technology allows the trainer to compensate immediately to belt misalignment, with the goal of the belt staying away from the structure and keeping the material on the belt.
Result:
With the PT Max’s ability to pivot and tilt, the belt began to run true immediately. The site changed out all the trackers on the belt, replacing each with a PT Max. This action removed all previous issues – including belt damage and spillage. By doing so, the site was able to save thousands of dollars in unscheduled downtime and belt repair. The site supervisor commented on the ease of dealing with Flexco, as well as their sound technical advice and short lead times. The PT Max was also customised to this specific conveyor and the site’s roller specifications, further contributing to the impressive results.