We’ve heard it time and time again. Doing the same thing over and over again and expecting different results is the definition of insanity. So let’s not pretend that installing and maintaining your belt cleaners the same way every time is going to produce a different result. Small changes, however, can prove very beneficial to your business – and also necessary to be able to progress, move forward, and create change.
The problem
A major iron ore site in Western Australia had an efficient belt cleaning system, but it wasn’t performing as well as it needed to. The site wanted the belt cleaners to last, maintenance-free for an 18 week period. However, the current secondary cleaners weren’t lasting the length of time they needed for the following reasons:
The tungsten carbide tips were underspecified for the application. Instead of selecting a cleaner with 25mm tips, which were more appropriate for handling iron ore, technicians at the site had specified a cleaner that was only available with 15mm tips. Because of this selection failure tips weren’t lasting the full 18 weeks.
The cushions for this cleaner were also under-specified for the site. They wouldn’t last the shutdown cycle and would fatigue before the expected maintenance time.
The solution
After performing a routine assessment on the site, our team decided to test a Flexco FMS Secondary Cleaner on the same 1800mm wide belt. The FMS is a heavy-duty secondary cleaner with long lasting tungsten carbide blades available with 25mm tips. The design of the new FMS cushion also allows for an increase in performance over traditional cushions used widely throughout iron ore applications in Australia.
The BIG results
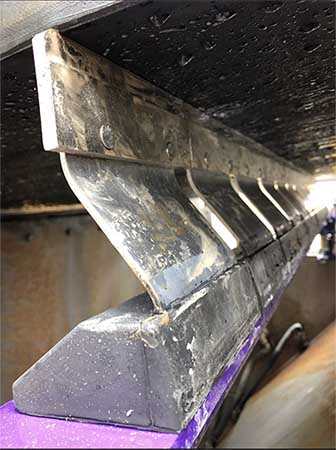 |
New FMS cleaner installed at the site |
The new cushions and tips lasted an amazing 36 weeks before being changed out during a regular shutdown, not due to fatigue. Because of the longevity of the new cleaner model, the site was able to save the labour cost of two service technicians, who were dispatched to the site for six hours each every 18 weeks. However, the site kept up with weekly visual inspections of the cleaner, weekly hose downs and tension adjustments – essential tasks to ensure any belt cleaner is working at an optimum. They were also able to save approximately $4,745 in replacement parts for each conveyor fitted with the FMS cleaner during the shutdown cycle.
Lessons learnt …
Having a third party assess your conveyor belt system for optimisation allows you to ensure product is being specified correctly and working it’s hardest. Remember, it’s important to walk each belt and choose products based on the particular specifications of each. Implementing coverall solutions for your site could do more harm than good. Each conveyor runs differently, with a variety of widths and belt speeds, so you’ll want to choose products that fit that each particular system. We also recommend using a third party to assess your system. Having a third party auditor perform an assessment on your conveyor belt system can ensure that your products are working their hardest to reduce not only carryback, but also lower maintenance needs and costs.
Authored by: Jayden Baker, WA/SA Territory Manager
Baker began working at Flexco in 2014 as a Territory Manager in Western Australia before taking the same management role for South Australia in addition to his current duties. He has worked in mining for 15 years, specialising in machine and automation safety. Baker holds qualifications in management, boiler making, and mechanical fitting.