In a conveyor operation, the fasteners holding the belt together are just a small piece of the production puzzle. So it’s not uncommon for there to be pressure to get repairs done as quickly as possible to limit downtime and get a system back up and running again. And while some crews have enough experience to install a good splice without reading the instructions, corners often get cut, resulting in a bad splice.
Why does a good splice matter?
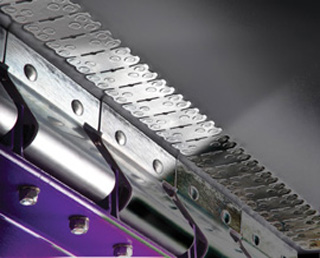 |
A properly installed splice will interact well with other components. |
You may be thinking that as long as the fasteners are holding the belt together and the material is moving along, the splice is just fine. And you may even wonder what the big deal is when it comes to installing a good splice. The big deal is that good splices will run longer, which ultimately leads to minimizing downtime. Unscheduled downtime due to splice failure can not only cost your operation time, but also money. Other than decreasing the overall life of the splice, some of the biggest problems that can occur with an improperly spliced belt include mistracking and damage to other conveyor components.
What to look for in a good splice
How do you even know if a good splice has been achieved? Well, there are a few things to look for when examining a splice and the splicing process:
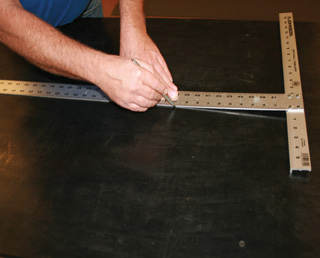 |
Flexco recommends the centerline method for squaring your belt. |
- A squared belt
This is the most essential part of a good splice. If the belt is not square when it is cut and a splice is installed, there will be uneven tension across the width of the splice. Since the tension is higher on one side of the splice, the fasteners or the hinge pin may not last longer than a properly squared splice. Another problem is that the belt will wander, causing mistracking. Not cutting a belt squarely is also one of the reasons a hinge pin may migrate out of the splice. We talk more about the importance of squaring your belt in this blog.
- Type of fastener
Depending on the type of belt you are running and the materials you are conveying, you’ll want to make sure you are choosing the correct fasteners for the job.Selecting the proper fastener involves taking three primary factors into consideration – belt tension, belt thickness, and pulley diameter – and then working from there to choose metals and hinge pins based on other factors like environment, application, and the type of material being conveyed. Proper fastener selection can even include deciding whether to choose hinged fasteners (good for small diameter pulleys because they reduce the pull at the joint) or plate fasteners (promote long wear and a sift-free splice).
- A smooth fastener transition|
This assessment is especially useful if there are cleaners on the belt. Skiving involves taking off some of the top cover of the belt to create a low profile and make the fasteners more compatible with the cleaners, encouraging a longer wear life for both the cleaners and the fasteners. Skiving also will reduce idler noise, minimize wear on idler bearings, and eliminate impact with skirting material. If the top cover of a belt is greater than 3/16’ (4.8mm) skiving is always recommended. Skiving does not affect the strength of the belt or the splice because only the top cover is removed, which does not affect the carcass. Deeper penetration of the fastener teeth into the belt carcass can also ensure maximum fastener retention rating. For more info on skiving your belt, check out this blog.
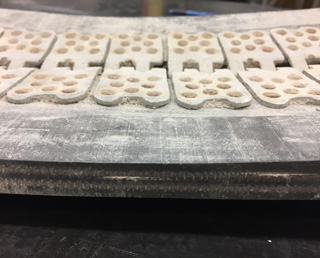 |
When fasteners are properly compressed, you should not see the edges like you do in this photo. |
- Fastener compression
To ensure you have adequate fastener compression, the finished splice should reveal no space between the bottom of the fastener plate and the belt surface. Good compression will create “belt pucker,” which occurs when the belt cover rises slightly above the edge of the fastener plate. You should not be able to get your fingernail under the plate, which is a quick test for compression.
There are plenty of tools that can help you ensure that your splices are the best they can be, including a proper belt cutter and belt skiver, but there is no substitute to making sure the job is done right, every time. You can’t be at every conveyor every time a splice is done, but you can make sure that you or a member of your crew is assessing your belt line from time to time. Better yet, contact your local Flexco representative for a free assessment and find challenges before they become problems that affect your productivity.
Shop Flexco Fasteners and Maintenance Tools
Authored by: Russ Heintz, Training and Technical Specialist
Russ Heintz has been with Flexco since 1995, working in various roles within the company before becoming Training and Technical Specialist. In this role, Heintz focuses on the efficiency of our products through in-house and field testing. Heintz also regularly conducts classroom and hands-on, internal or on-site training with Flexco employees, distributors, and customers.