Keeping conveyor systems running efficiently is essential for any operation that relies on belt-driven material handling. But while most facilities focus on maintaining their belts and conveyor components, the equipment used to splice those belts is often overlooked—until it fails at the worst possible time.
For distributors of endless splicing equipment, a proactive approach to maintenance isn’t just beneficial, it’s required. When your press isn’t working properly, it can lead to poor splice quality, sanitation risks, safety hazards, and worst of all, costly downtime for your customers. If you haven’t checked in on your endless splicing equipment in a while, now is the time.
Here’s why proactive maintenance matters and how it can help protect your business, your customers, and your reputation. 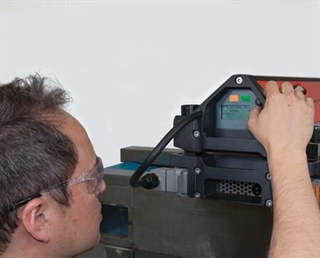
The Hidden Risks of Poorly Maintained Splicing Equipment Compromised Splice Quality and Belt Performance
A seamless splice is crucial for belt longevity, performance, and hygiene, especially in industries like food processing, where belts must meet strict sanitation requirements. If a press isn’t performing correctly, it can create weak or incomplete splices, leading to belt failures, mistracking, and product contamination.
Poor-quality splices increase material buildup at the seam, making it harder for any installed cleaning systems to remove debris. Over time, this can lead to regulatory compliance issues, product recalls, or even health risks in food production environments. Having a well-maintained press helps prevent these issues before they even start.
Increased Safety Risks for Operators
When splicing equipment is neglected, the risk to operators rises significantly. Malfunctioning presses can overheat or break down unexpectedly, putting technicians at risk of handling hot or faulty components.
For example, electric pins and Harting connectors in advanced presses like the Novitool® Aero® Splice Press should be regularly inspected to prevent wear-related failures. Failing to do so not only jeopardizes safety, but it can also take an essential tool out of commission right when you need it most.
Unexpected Downtime and Lost Revenue
The real cost of poor maintenance becomes painfully clear when a splice press breaks down mid-job. Picture this—your maintenance crew travels to an end-user facility, sets up their splicing equipment, and suddenly realizes their press isn’t functioning properly.
At that point, you’d be facing hours or even days of unplanned downtime while you scramble to find a replacement. As a result, your customer’s operations are disrupted, deadlines are missed, and the reliability of your service is called into question.
A proactive maintenance plan ensures this scenario likely never happens.
How Proactive Maintenance Protects Your Business Extend the Life of Your Splicing Equipment
Simply put, routine maintenance significantly extends the lifespan of your splice press. By keeping key components fresh and in working order, you avoid premature failures and ensure consistent, high-quality splicing performance for years to come.
With advanced presses like the Novitool Aero, reviewable cycle logs and performance data can give users early warning signs of wear and tear before issues arise. Checking this data regularly allows you to proactively plan maintenance before failures occur, rather than reacting to a downtime incident.
Reduce Downtime and Keep Your Customers Happy
Distributors who implement a proactive maintenance strategy are better equipped to meet customer demands. By ensuring that your splicing equipment is always ready for use, you avoid delays, reduce unexpected service disruptions, and build trust with your customers by always completing the job.
For some larger operations, downtime can cost over six figures per hour. Keeping a reliable, well-maintained splicing system in place can mean the difference between a smooth production run and a catastrophic delay that impacts both your revenue and your reputation.
Get Ahead with the Proactive Maintenance Plan
If it’s been a while since your press was inspected, the time to act is now.
Flexco’s Proactive Maintenance Plan allows distributors to send in their equipment for a full inspection and undergo system optimization that is conducted by specially trained product experts.
Through this program, our team conducts a deep dive into your equipment, analyzing performance logs, testing key components, and making informed decisions on the best course of action for your maintenance teams. If any repairs or replacements are deemed necessary, recommendations will be made.
Our team even offers a loaner press unit to you during the inspection process, allowing you to continue to serve your customers and complete crucial jobs while your unit is being serviced.
Learn More
Stay Ahead of Maintenance Before It Becomes a Problem
Being proactive about maintaining your endless splicing equipment doesn’t just protect your machinery, it protects your business, your customers, and your bottom line.
Instead of waiting for a press to fail, take action now. A well-maintained system ensures that you deliver high-quality splices, avoid unexpected downtime, and maintain a strong reputation as a reliable distributor.
Don’t let maintenance become an afterthought—make proactive maintenance part of your success strategy.
Be Proactive
Authored by: Michelle Graves, Product Manager
Graves manages the overall global business, market plans, technical support, and activities associated with the light-duty belting market for the Novitool product line, including new product development, market analysis, and global strategy. Graves holds a bachelor’s degree from Albion College as well as a master’s degree from Grand Valley State University.