When you’re on the job, day in and day out, common belt conveyor problems can go unnoticed because you aren’t actively looking for them. But a quick visual inspection can mean the difference between a productive day and a costly day for your aggregate operation.
Listed here are the Top 10 conveyor challenges that you can identify with a simple visual inspection, what problems they can cause, and how to fix them in a short period of time.
Look for: Damage to belt cleaners, premature wear of fasteners, carryback, mistracking of the belt.
Causes: Unskived splices, fasteners interfering with the cleaners.
Solution: Skive your belt before applying splices, when possible, and use low profile fasteners with a coined edge. Make sure all manufacturer’s instructions are followed when splicing, including proper squaring of the belt.
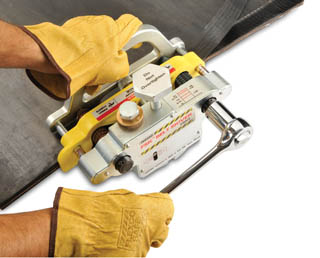
If you notice your fasteners are wearing prematurely, skiving your belt may be the key to longer splice life.
Look for: Premature belt splice failure, uneven lagging wear, early cover wear at trough line.
Causes: Poor transition distance.
Solution: Check your transition distances. Verify that your transition distances are in line with CEMA standards. For fabric belts, CEMA typically recommends a transition distance of 4.0 x the belt width.
Look for: Belt ripping right behind the splice, premature belt failure.
Causes: Fasteners that are too large for the smallest pulley.
Solution: Check the minimum pulley (where the belt wraps 90 degrees or more) diameters against both the belt manufacturer’s recommendations as well as the fastener manufacturer’s recommendations. Using a pulley diameter that is smaller than the belt and/or fastener’s recommended size can produce excessive bending stresses with the possibility of belt splice failure.
Look for: Belt slippage.
Cause: Small pulleys.
Solution: The proper pulley diameter is crucial to belt performance. When it comes to slippage, the surface area where the belt goes from full tension (top) to partial tension (bottom) and “shrinks” puts an extensive amount of pressure on the lagging to move with it and prevent slip. While CEMA does not specifically recommend a pulley diameter by application, the engineers of conveyor systems make recommendations for pulley diameters based on the design of the conveyor. Often, the small pulley will be substituted to save costs without consideration for this belt shrink – if they minimize the pulley size, they also minimize the area in which the lagging can help the belt shrink as it wraps around the pulley. Reduce the size of the pulley this too much may cause slippage.
Look for: Mistracking, poor splice life.
Cause: Improperly squared belt.
Solution: Square belt using appropriate tools. Squaring the belt involves marking the center of the belt at 3 to 5 foot intervals for approximately 20 feet from the splice area, drawing a center line based on those markings, and using a square to draw a line that is perpendicular to the average center line across the belt width. Don’t forget to use a proper belt cutter (as opposed to a utility knife) for a safer, straighter cut.
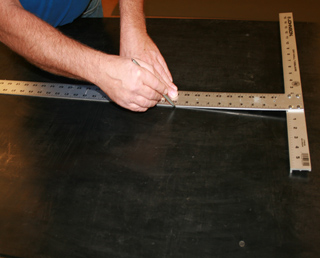
Sometimes quick fixes can be prevented. A properly squared belt can extend the life of your belt and help avoid mistracking.
Look for: Spillage at the load zone.
Cause: Poor skirting, no impact protection.
Solution: Check and maintain skirting with easy to use system. Skirting is important in the load zone because it stops material spillage leaks, controls dust emissions and eliminates other resulting problems such as belt damage and mistracking. Seek out a skirting system that is easy to service and has corrosion resistant components for less maintenance. You will also want to ensure that the proper impact protection is available and the belt is properly supported in the load area. Your impact protection should take into account lump weight and drop height, and should deliver maximum protection to your belt in the load zone.
Look for: Belt damage, conveyor structure damage.
Cause: Belt mistracking.
Solution: Identify the cause of the mistracking and install a belt trainer. Misalignment of rollers or pulleys, an incorrect splice, and material buildup are just a few of the things that can get your belt off track. Friction and tension have been proven to provide effective tracking when utilized together. Choose a tracker with a pivot and tilt design that provides friction and changes the tension profile of the belt.
Look for: Belt damage from seized rollers.
Cause: Seized rollers cut into belt.
Solution: Regularly inspect conveyor for seized (non-rotating) rollers. For steel rollers, look for flat spots with sharp edges; these should be replaced immediately or risk cutting the belt. For composite rollers with a steel core, look for flat spots with sharp edges; these should be replaced immediately or risk cutting the belt. For composite rollers without a steel core, replace when feasible.
Look for: Belt cleaners not working properly.
Cause: Incorrectly mounted cleaners or belt cupped when passing by cleaners.
Solution: Ensure that the cleaners are mounted correctly by reviewing installation instructions. If the belt is cupped, introduce a hold down roller to flatten the belt and ensure proper cleaner to belt contact.
Look for: Poor cleaning edge and a dirty belt.
Causes: Poor attack angle, worn blade, or incorrect blade in reference to the material path.
Solution: Pole location is vital to the success of the cleaner because it permits the correct blade attack angle, encourages maximum cleaning performance, and ensures maximum blade life because the entire wear area of the blade can be used. Optimal cleaning can be attained by paying close attention to the material path of the belt, which is typically the center 2/3 of the belt width. Choosing a blade that is only slightly wider than the material path can decrease blade wear and replacement.
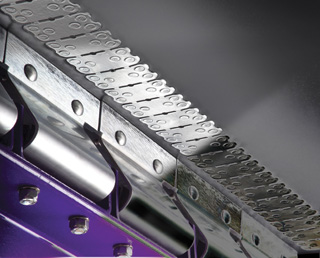
Ensuring that your belt conveyor components are compatible with each other is key to all parts running smoothly.
Along with visual checks every day, operations should perform a yearly belt conveyor audit. The audit can be done by an internal team, but participation by a third party is helpful. Simple maintenance tasks that may have gone unnoticed can be identified and addressed by your team, or components can be replaced that will make your equipment run more efficiently. If nothing else, an audit can help keep your equipment running longer.
Over time, carryback, spillage, improper fastener selection, and mistracking can cause serious problems for your belt conveyor system. Although these may seem to be everyday issues, solutions are available and are integral to your operation’s success. All too often, plant operators don’t even realize there’s a problem until production is halted. In the end, it all affects the operation’s bottom line. Don’t let that happen to your operation.
Authored by: Ryan Grevenstuk, Director of Marketing – Heavy Duty
Grevenstuk is responsible for strategic global business and market plans, industry and market research, new product development, customer relationship management, and technical support for the heavy-duty product lines at Flexco. He holds a bachelor’s degree from Central Michigan University, as well as a master’s degree from Western Michigan University.