I think everyone can agree that the holiday season is the most important time of the year for logistics operations. And this year, more than ever, parcel, warehousing, distribution, and fulfillment facilities are busier. This is the time when additional people are hired, throughput goals are increased, and overall production is ramped up.
But this year, it feels like we have been ramped up for 18 months already because of increased demand, supply chain delays, hiring challenges, and increased unscheduled absences due to COVID-19.
Can we possibly ramp up MORE?
It may seem impossible, and it might be in regards to the issues we already laid out, but there is a way you can ramp up your production that doesn’t involve these issues … efficient maintenance of your belt conveyor systems. If you’re reducing the downtime associated with maintenance activities, you are able to get back to producing throughput more quickly and your team can focus their time on proactive maintenance repairs.
Below are two common conveyor maintenance challenges that can be addressed to maximize the throughput and productivity of your operation.
Optimizing your conveyor transfers
Conveyor transfer gaps are areas contributing to one of the biggest causes of conveyor downtime in the logistics industry. The gaps can lead to small packages (and their contents) being caught in the gaps between conveyors, which leads to conveyed product damage or product loss.
For this reason, pop-out rollers are often placed in transfers on conveyor designs to avoid these problems, but pop-out rollers can sometimes do more harm than good. (For more information on this, check out the blog I penned all about pop-out rollers and why they should be a thing of the past in modern-day conveyor systems. Spoiler alert! They pop out too often and too easily!)
Pop-out rollers aren’t the only things I’ve seen as a solution to package jams. Oftentimes, operations try homemade solutions like bolting a piece of UHMW to angle iron at the transfers to keep items from getting stuck in them. But damage to the belt and conveyor system components are oftentimes the only results that are seen when this plan is deployed – you can learn some of the other reasons why homemade solutions aren’t optimal in this blog.
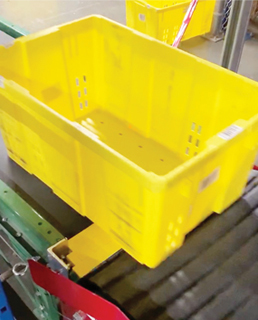 |
A tote slides effortlessly across the transfer after installation of a Flexco Segmented Transfer Plate. |
The truth is that an engineered solution is the best answer to your challenges, with longer wear-life, easier maintenance, and less downtime. Flexco’s Segmented Transfer Plate accomplishes all that and more, adding the benefit of segments. Each plastic segment is positioned directly on the belt, which prevents product ingestion and reduces nip points and pinch hazards. When installed properly, the light seal against the belt prevents items from becoming lodged between the belt and the plate. In the rare event the contents of a package does get in between the segment and the belt, the segment will lift, allowing smaller items to fall through or eject under more extreme circumstances. The plate can then be repaired in seconds by simply snapping a new segment in place, resulting in no damage to the belt, conveyor structure, or packages, while significantly reducing conveyor downtime.
Minimizing live roller conveyor repair downtime
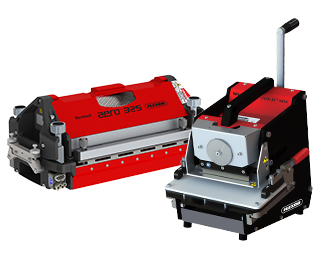 |
The Novitool® Pun M™ NDX Mobile Finger Punch and Aero® 325 Splice Press, make punching and splicing a live roller belt quicker, easier, and safer |
The transmission belts that drive your live roller conveyors are the heart of your operation. When one of those belts goes down for a repair, panic can set in as you wonder, “how long will this repair take and how much is production going to be affected?” If your current method of punching and splicing isn’t getting the job done in 18-20 minutes, you have the chance to optimize your belt repair process as well.
With the Novitool® Pun M™ NDX Mobile Finger Punch and Aero® 325 Splice Press, repairs of the belts that drive your live roller conveyors will be done 66% faster. You can increase the efficiency and productivity of your belt prep with the easy-to-use Novitool Pun M NDX Mobile Finger Punch. Its single heavy-duty blade ensures precise cuts, with little to no fraying of cords, while the belt support table automatically realigns to ensure automatic re-indexing without stopping for adjustments.
With splice times as quick as 18 minutes from heat up to cool down, the Novitool Aero 325 Splice Press can repair a live roller or transport belt, as well as other thermoplastic PVC or PU belting, in a third of the time of traditional splice presses. The Aero 325 is easy to use, portable, and produces consistent, repeatable, quality splices every time.
As you have probably already guessed, we also have blogs on belt punching and splicing best practices that will give you even more information on how to make the belt repair process quicker, easier, and most importantly, safer.
Focus on the things you CAN control
It’s easy to dwell on the things we can’t control instead of focusing on the things we can. While we can’t wave a magic wand and make employee shortages and supply chain nightmares disappear, we can proactively take a look at our systems and find better ways to do things that allow us to increase our throughput and makes better use of the employees we do have on board. If you’re interested in having a second set of eyes assess your conveyors to help you find ways to maximize your productivity, a Flexco expert is more than willing to come out and take stock of the health of your conveyor transfers, splices, and lacing equipment. Click here to sign up for a free assessment today.
Authored by: Todd Stewart, Industry Manager
Stewart focuses on both the logistics and food processing industries, creating programs to support each segment and identifying customer issues, as well as potential product solutions, for industrial baking, confectionery, parcel, airports, warehousing, distribution, and fulfillment. Stewart began his career at Flexco in 1989, working in various roles from customer service, to manufacturing, to training, to new product development, to market development management before taking on the role of Industry Manager in 2017. He earned a bachelor’s degree in Marketing with a B2B specialty from Davenport University.