Earlier this year, eMarketer released some stats and trends to watch for 2021 in relation to global ecommerce. And while 2020 took a drastic 27.6% leap up the charts because of the pandemic, growth will remain steady through 2024. This year, ecommerce sales are expected to total $4.89 trillion, with 2024 projected to be at $6.38 trillion.
So what does all this mean for your parcel handling operation, warehouse, or fulfillment centers and distributor centers? It means business will be good for a VERY LONG TIME.
Once you get past the euphoria of booming business, the panic may be creeping in with your next thought being, “do I have the personnel for this and can my equipment hold up to this increased volume?”
Taking a closer look at your belt conveyor system
Let’s first focus on what we know best – belt conveyor equipment. Instead of eyeing your capital equipment budget for opportunities to purchase large machinery, maybe you should take a look at something a little more budget-friendly that can make an immediate impact on downtime, worker safety and fatigue, and throughput … upgrading your belt conveyor maintenance tools.
When was the last time you looked at how a belt is repaired and thought, “There has to be a better way?” The truth is, you probably haven’t. Because the methods for installing mechanical fasteners have not changed much throughout the years. And with the exception of a few, the tools used to install them haven’t either. But in some cases, there are better ways that you probably haven’t noticed because, well, you’ve been busy.
Preparing your conveyor belt for quick and safe repair
The opportunity begins with maintenance tools. When I think of preparing my belt for safe repair, a three-word phrase mantra runs through my head over and over again:
Clamp, Square, Cut. Square. Cut. Clamp. Clamp. Square. Cut. (The steps can be different depending where you are preparing the belt.)
It can get really catchy when you put a beat to it.
But in all seriousness, there are opportunities for productivity-enhancing opportunities within all three of these steps. Let’s take a look:
Clamp. The first, and most important function of proper belt clamping is that it provides a safer working environment for your employees. Where your productivity-enhancement comes in is your choice of belt clamps. For example, if you’re using the old bolt-actuated method, consider upgrading to a safer, more efficient tool that clamps down quickly and easily. Flexco SmartClamp™ Belt Clamps ensure clamping pressure is evenly distributed at each clamp, keeping belt integrity intact and maintenance hazards at a minimum.
Square. When you square the belt correctly, you reduce the chances of your belt mistracking to one side and damaging your belt or the packages it is carrying. No one wants their belt to go down because a line was drawn incorrectly. The Laser Belt Square from Flexco makes the process of squaring a belt for splicing fast and easy, and the line is much more accurate than using a carpenter square at the edge of the belt … especially when working with a worn belt.
Cut. Grabbing the utility knife out of the toolbox is tempting, but the truth is, it is a safety and accuracy nightmare. Remember what we just said about the importance of squaring? Cutting with a utility knife could ruin your chances of a straight cut, meaning mistracking is in your future. The Flexco 845LD Belt Cutter produces a straight cut every time. Plus, as a bonus, it has an enclosed blade, which also makes it the safer option for your employees. Employee injuries are scary but preventable in most cases. In a worse case, a severe cut from a razor knife at the conveyor can could cause a stop in production for the rest of the shift.
Upgrading your installation tools
Now that you’ve been able to speed up your belt prep time, we can focus on upgrading your fastener install tools. I’m going to guess your fastener of choice is a high quality Clipper® Wire Hook, so that’s what we’ll focus on here.
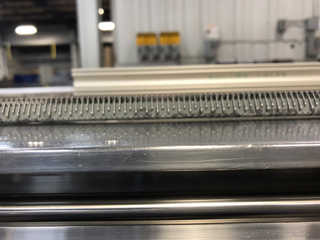 |
Clipper® Wire Hooks in Clipper® Roller Lacer
|
The Clipper® Roller Lacer® revolutionized the industry back when it was introduced in the early 1980s. And the premise of how it works is the same today as it was then, with a few upgrades along the way. If you have an original Roller Lacer (yep, they are still out there), you might have to take a few more passes along the belt than you would if you upgraded to a new one. You may also have to perform a few extra steps that involve locking levers and back up bars. Those steps have been eliminated with a redesign of the face strips.
If you want to save even more time, the Roller Lacer® Gold Class™ features high-speed installation that completes splices 30-50% more quickly by using a cordless drill to drive the lacer head. Even though most people love the speed, the most popular feature of the Gold Class is the belt support shelf, which helps guide the belt into the hook points for quick and easy set-up.
Quick Tip: Installing Clipper® Wire Hooks on a bias spreads the belt tension across a longer area and reduces environmental noise. See the video below to learn how to install Wire Hooks on a bias using the Clipper® Roller Lacer® Gold Class™.
Now about hiring new people …
I can’t really give you any advice on how to recruit and hire the best people, but what I can tell you is that good safety and ergonomic practices can be a really big job differentiator, especially when you are neck-in-neck on salary. And everything we’ve talked about in this blog makes a current and potential employee’s job safer and easier.
And when you do end up getting all those employees hired and are starting the training process, we can help with that too … for FREE. It’s true. If you need training on anything from the maintenance and installation tools we just discussed, to best practices for protecting your conveyor transfer points, to tips and trick for quality endless splices, click here and we will set up in-person or virtual training.
Stewart has been with Flexco for over 32 years, working in various roles from customer service, to manufacturing, to training and new product development. As Industry Manager, Stewart thoroughly researches target industries, creating programs to support each industry and identifying customer issues, as well as potential product solutions. Stewart currently leads the development of the Logistics Industry Program and is responsible for ensuring that Flexco is positioned to serve the needs of our global customers. Stewart earned a bachelor’s degree in Marketing with a B2B specialty from Davenport University.