It’s early November. Crisp autumn air replaces the warm air of late summer. Entering the facility, you can’t help but notice early signs of the pending peak Christmas shopping season. Teammates from other departments are scurrying to make their final push of their pre-peak preparations smile and say “hello” as you pass. There is a subtle tension building as you remind yourself of the pain points in your conveyor system you wanted to address before peak. You address what you can. Some issues you just live with.
Some issues you think you HAVE to live with when you really don’t – but we’ll get to that later. 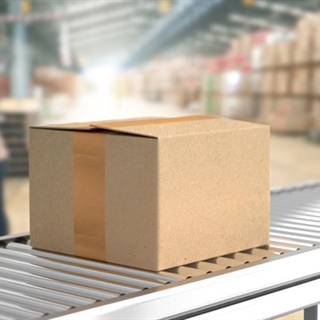
Soon there will be a flood of small packages, polybags, and jiffy packs flowing down your conveyors. Mariah Carey’s Christmas CD, a Barbie doll, an adjustable wrench, and a small bottle of perfume … all headed in individual packaging to a home or business to help make someone’s Christmas bright.
Unless, of course, the gifts don’t make it.
It’s very common to see piles of small packages building up under roller conveyors as you walk through a facility, especially during peak times. Some of them are motor-driven roller conveyors with bands transferring the power to non-powered rollers. Some are belt-driven live roller conveyors. All offer the potential for package jams, packages falling through the gaps between rollers, and the potential to pinch workers fingers between the rollers and the belt or band. Thousands of dollars of potential output just piling up in their usual places on the floor below the conveyor. Packages late or damaged, and soon to be unhappy customers waiting for packages that didn’t arrive on time, or at all. The issue is only getting worse with the movement away from boxes and towards a bag of some sort.
It is fitting that I share this real-life horror story during this autumn season. Halloween is lurking in our rearview mirror and scary things abound. It has been a similar story for your system every year.
Remember when I mentioned that there are some things you think you HAVE to live with, but you don’t really? Hold on to your hat, because we’ve got a solution.
Just in time for peak season, Flexco is releasing an easy-to-install, simple fix to your roller conveyor problems. The Roller Conveyor Transfer Plate (RCTP) is coming. Closing gaps will be done in a “snap”. Closing your eyes for a restful sleep during peak season will follow.
For now, keep your eyes open for the unveiling of Flexco’s Roller Conveyor Transfer Plate. And breathe … your horror story may just have a happy ending.
Authored by: Todd Stewart, Industry Manager
Stewart focuses on both the logistics and airport industries, creating programs to support each segment and identifying customer issues, as well as potential product solutions, for parcel, airports, warehousing, distribution, and fulfillment. Stewart began his career at Flexco in 1989, working in various roles from customer service, to manufacturing, to training, to new product development, to market development management before taking on the role of Industry Manager in 2017. He earned a bachelor’s degree in Marketing with a B2B specialty from Davenport University.